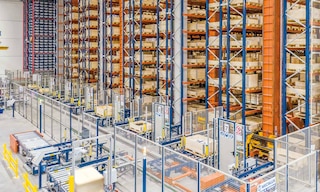
Os PLCs em logística, primeiro passo para a automação do armazém
O crescimento dos controladores lógicos programáveis (PLC em inglês ou CLP em português) em logística tem acompanhado a automação de armazéns e fábricas. Trata-se de processadores robustos cuja função é executar um programa de automação em ambientes logísticos e industriais.
Portanto, são dispositivos que se encarregam de processar as instruções e de executar os movimentos programados para que a instalação automática funcione corretamente.
O que é um PLC ou controlador lógico programável?
O controlador lógico programável (em inglês, programmable logic controller) é o primeiro obstáculo da automação industrial. Muitos sistemas automáticos do armazém contam com um processador industrial PLC que facilita a automação de seus movimentos. É importante não confundir as siglas PLC no contexto da robótica com o Power Line Communications, ou seja, a tecnologia que permite trocar informações através de linhas de alta tensão.
O funcionamento do PLC é o seguinte: o processador estabelece comunicação com um software de nível superior, que processa as informações recebidas do software de gerenciamento de armazém e executa as tarefas em função de regras pré-programadas. Esse tipo de microprocessador, geralmente mais robusto que um PC, opera em tempo real: recebe as informações pelos canais de entrada e executa os movimentos da máquina pelos canais de saída.
Componentes de um PLC
Os PLCs possuem uma estrutura básica, semelhante à de um computador, formada por:
- CPU: unidade central de processamento que interpreta cada uma das instruções programadas.
- Fonte de alimentação: componente que fornece energia elétrica à CPU e aos demais elementos do PLC.
- Módulo de memórias: espaço disponível do processador onde guarda todas as informações necessárias para executar a tarefa de controle.
- Entradas e saídas: módulos analógicos e digitais que garantem o sucesso na execução do PLC. As entradas processam as informações do software superior, enquanto as saídas permitem a conexão física entre o computador e o robô que deve ser movido.
- Unidade de programação: conjunto de hardware e de software que permite ao PLC interpretar em uma ou outra linguagem de programação as instruções recebidas de outro programa.
Como curiosidade, esses autômatos são programados mediante linguagens como Ladder, muito populares nesses equipamentos, baseadas em diagramas de contato e esquemas de controle clássicos. Nos últimos anos foram incluídas as linguagens IEC que facilitam o uso de um mesmo programa em PLC de diferentes fabricantes.
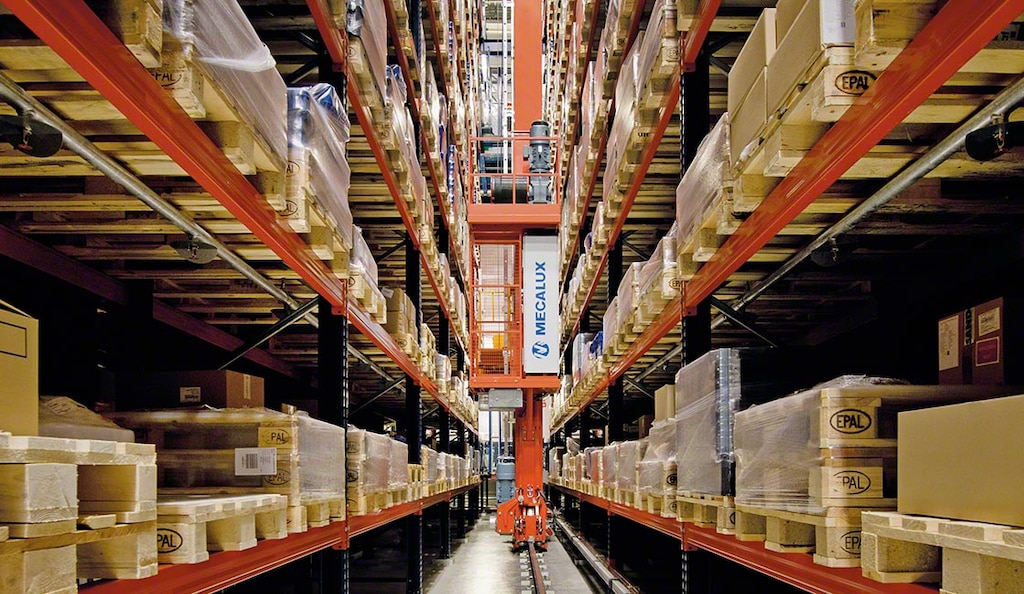
Diferenças entre PC e PLC
É comum confundir os controladores lógicos programáveis (PLC) com os diferentes PCs de controle que existem em qualquer posto de trabalho de um armazém, pois os dois podem controlar os movimentos de um robô industrial a partir das informações recebidas por um software superior. Além disso, ambos os hardwares possuem uma estrutura semelhante: uma CPU, um conjunto de sinais de entrada, sinais de saída e memória.
No entanto, os controladores lógicos programáveis (PLC) não contam com um sistema operacional, impossibilitando a utilização de banco de dados. Pelo contrário, um PC funciona com um Sistema Operacional, onde se instala um software como o Galileo (utilizado pela Mecalux em suas instalações), que coleta informações sobre o status da instalação e recebe instruções para ativar o movimento dos sistemas automatizados.
De qualquer forma, um PLC proporciona inúmeras vantagens em relação a um PC preparado para a atividade industrial: oferece a possibilidade de incluir programas de segurança com entradas e saídas mais seguras, ideais para os processos que não admitem margem de erro.
Além disso, os controladores lógicos programáveis (PLC) são uma ferramenta perfeita para o setor logístico e produtivo, porque são mais robustos e foram especialmente projetados para contar com proteção em ambientes complexos (com vibrações de alta frequência, corrosão ou mudanças de temperatura).
A Mecalux utiliza uma combinação de PC e PLC em suas instalações, aproveitando os benefícios oferecidos por cada um desses dispositivos.
Funções e aplicações dos PLCs em armazéns
Os PLCs servem como primeira engrenagem para a automação de um armazém, uma vez que atualmente é utilizado em qualquer lugar onde exista um sistema robótico. Esses processadores robustos operam como um computador de mesa, exceto se suas funções estiverem particularmente adaptadas a ambientes industriais. Por quê? Os sistemas operacionais utilizados pelos computadores são menos estáveis que os PLCs, além de não terem sido especificamente projetados para resistir às condições de trabalho das indústrias e armazéns.
Os PLCs costumam ser instalados em processos industriais que exigem pouco espaço, um controle de processos ou que utilizem várias sequências para realizar diferentes tarefas. Devido à sua alta resistência são a ferramenta adequada para executar os movimentos automatizados de um armazém: desde os robôs pick and place das estações de picking na indústria automobilística até os sistemas automatizados de armazenamento de mercadoria em setores como o químico ou o farmacêutico. De fato, uma ampla maioria dos sistemas automáticos de armazenamento ou transporte, como os miniload ou transportadores para caixas, são controlados através de PLC.
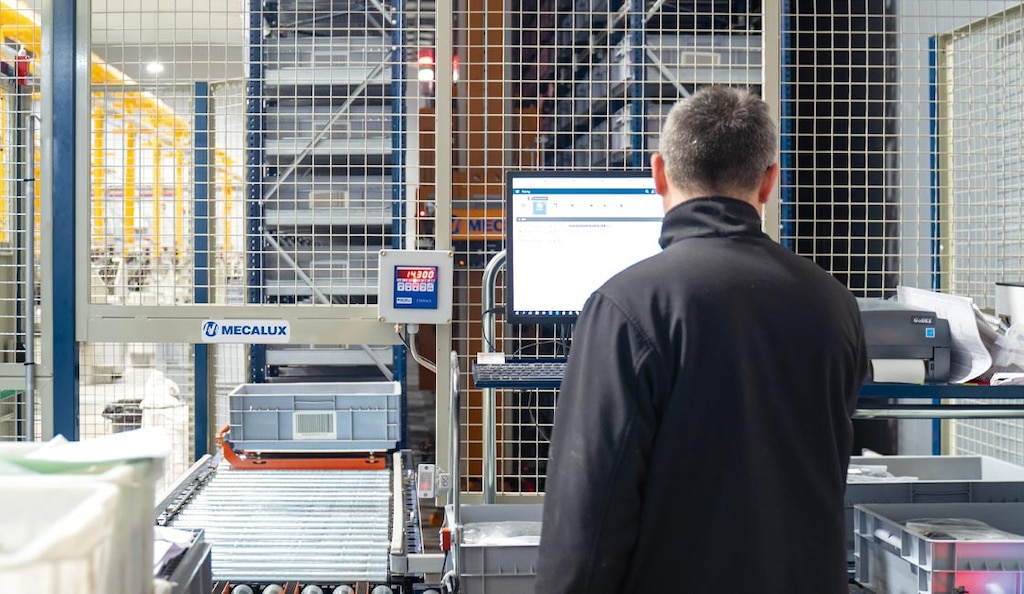
A relação entre PLC, WCS e WMS
Um PLC é o hardware onde está localizado um programa especializado que interpreta as informações recebidas de um software de nível superior e executa os movimentos através de sistemas automatizados.
Por outro lado, um WCS (warehouse control system) é o software de nível superior que envia dados ao PLC ou ao PC industrial para que este se encarregue de mover a maquinaria. Esse programa informático comanda os elementos que controlam a saída de mercadoria e o gerenciamento de localizações. Portanto, controla desde o percurso dos transelevadores para paletes até as cabeceiras de picking, passando por qualquer elemento automatizado.
No entanto, ainda existe um terceiro programa logístico que opera como ‘cérebro do armazém’: indica ao WCS as diretrizes que devem ser enviadas aos PLCs de acordo com os critérios de localização, as estratégias de picking ou as rotas parametrizáveis de expedição, entre muitas outras variáveis. Esse software é o Sistema de Gerenciamento de Armazém (WMS).
PLC, um dos pilares da automação industrial
Seja através de PLC ou de um PC com um software integrado, a coordenação entre os diferentes sistemas automatizados é fundamental para proporcionar eficiência e produtividade a um armazém. Além disso, é preciso adicionar que a automação industrial é cada vez mais real nos centros logísticos: se prevê que o volume de negócio desse setor até 2026 supere a cifra de 30 bilhões de dólares, segundo o último estudo da consultora Logistics IQ.
Nesse contexto, o bom funcionamento do armazém automático passa por contar com sistemas que garantem a sincronização entre todos os sistemas automatizados, promovendo a segurança, a produtividade e, sobretudo, a eficiência da instalação.
A Mecalux conta com uma equipe de profissionais para projetar e implementar armazéns automáticos adaptados ao seu produto, à sua instalação e às suas necessidades. Não hesite em entrar em contato conosco, um consultor especializado terá prazer em assessorá-lo para lhe oferecer a solução mais adequada para melhorar seu desempenho logístico.