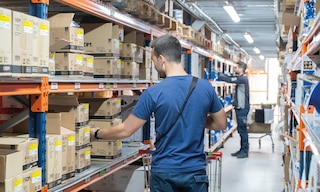
Picking por área: divisão eficiente para a preparação de pedidos
Como melhorar as operações de picking para reduzir os deslocamentos desnecessários dos operadores e aumentar sua produtividade? Uma das estratégias para consegui-lo é o picking por área, um método de preparação de pedidos que consiste em dividir o armazém em diferentes áreas, atribuindo cada área a um ou vários operadores. O objetivo dessa estratégia é reduzir as distâncias percorridas pelos trabalhadores dentro do armazém para fomentar a eficiência na preparação de pedidos.
Neste artigo explicamos o que é o picking por área, seus principais benefícios e desvantagens, os tipos de armazém ou centros logísticos em que pode ser aplicado e, sobretudo, como implementá-lo.
O que é o picking por área?
O picking por área (conhecido em inglês como zone picking) consiste em dividir a área de armazenamento em diferentes setores seguindo vários critérios, tais como o tipo de produto, o nível de demanda, as condições de armazenamento ou a quantidade de referências. Para cada área é atribuído um número de operadores que se encarregam de fazer o picking de qualquer produto que esteja em sua área, o que otimiza o tempo de preparação de pedidos.
O picking por área costuma ser implementado em empresas com um alta quantidade de pedidos heterogêneos, como os e-commerce, onde cada pedido pode conter artigos de diferentes tamanhos, uso ou seção. Setorizar a localização de produtos permite evitar movimentos desnecessários de operadores e mercadorias pelo armazém.
Tipos de picking por área: sequencial ou simultâneo?
Para implantar o picking por área o armazém é dividido em áreas e para cada uma delas se reserva um número determinado de operadores. Quando um pedido exige produtos de várias áreas, esse método de picking pode ser sequencial ou simultâneo, em função do número de pedidos realizados ao mesmo tempo.
Picking por área sequencial (pick and pass): através desse método só há um contêiner por pedido que percorre as diferentes áreas (através de um transportador, por exemplo). Os operadores encarregados de cada área de armazenamento depositam no contêiner os artigos indicados na guia de remessa ou no terminal de radiofrequência. Quando o contêiner chegar ao final do percurso, o pedido já está consolidado.
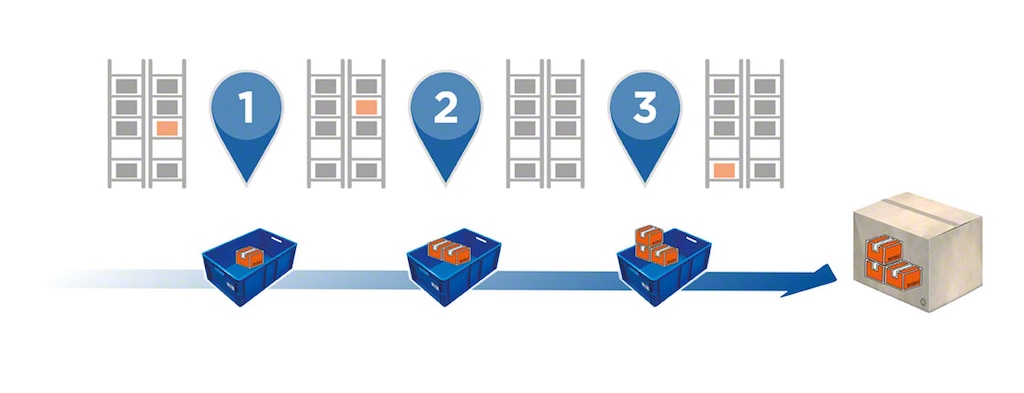
Picking por área simultâneo (pick and merge): nesse caso, os operadores de cada área trabalham em um mesmo pedido simultaneamente, cada um com seu próprio contêiner. Dessa forma, o operador de uma área não precisa esperar que o da área anterior tenha terminado para poder trabalhar no pedido. Quando todos os operadores tenham finalizado sua tarefa, o pedido acaba de ser consolidado em outro espaço (os produtos provenientes de diferentes áreas são agrupados e pertencem ao mesmo pedido). Ao não haver interferências entre operadores, essa estratégia permite ganhar tempo e agilizar o processo final de embalar.
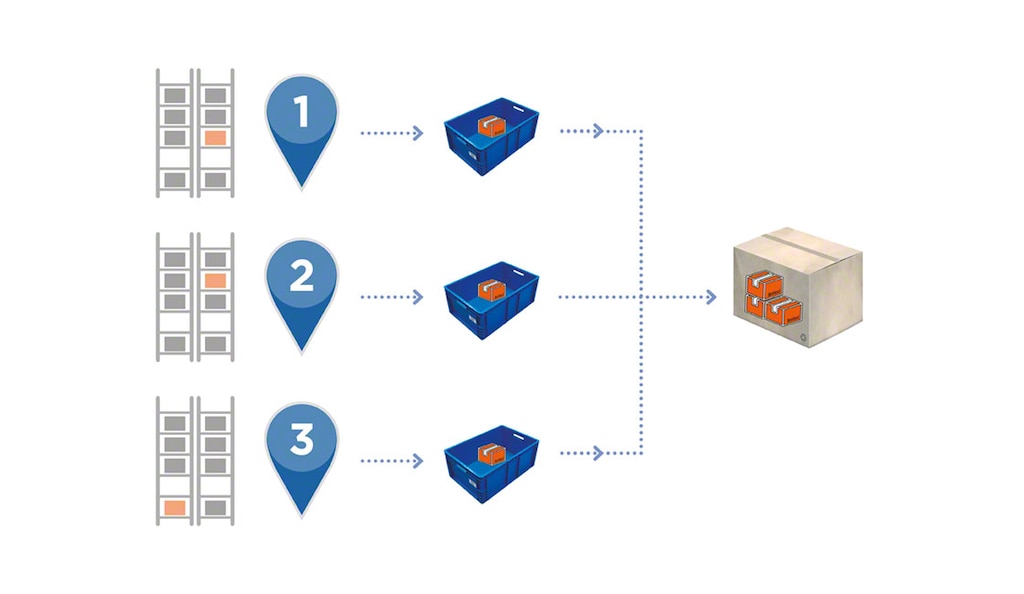
Vantagens e desvantagens do picking por área
O picking por área garante:
- Percursos eficientes. Reduz os movimentos dos operadores no armazém, permitindo que eles realizem o máximo número de pedidos no menor tempo possível.
- Rapidez e redução de erros. O Sistema de Gerenciamento de Armazém indica a quantidade de artigos que o operador deve localizar em cada contêiner, acelerando suas tarefas e limitando os erros que possam ocorrer.
- Eliminação de congestionamentos. O picking por área permite uma melhor organização do armazém. Menos percursos realizados pelos operadores no armazém evitam congestionamentos e previnem acidentes.
- Slotting produtivo. A segmentação do armazém em várias áreas garante uma melhor organização no gerenciamento das localizações, assim como reduz os pontos de estrangulamento. O WMS automatiza o gerenciamento das localizações no armazém (slotting) garantindo que a localização e a extração de mercadoria se baseiem em critérios predefinidos pelo responsável logístico.
- Gerenciamento eficiente com uma alta densidade de referências. A setorização é perfeita para armazéns com um alto número de referências, uma vez que limita o risco de erros e movimentos desnecessários feitos pelo pessoal.
- Especialização dos operadores. A divisão do armazém em áreas permite treinar os operadores quanto às características e condições do setor atribuído para obterem um conhecimento mais profundo do produto e uma maior produtividade.
- Versatilidade. Esse método pode ser combinado com outros sistemas de preparação de pedidos quando o responsável logístico considerar necessário, tais como o batch picking, o wave picking ou os sistemas de preparação de pedidos semiautomáticos.
No entanto, também é preciso considerar os inconvenientes. A implementação do picking por área implica uma limitação da flexibilidade diante de picos de demanda inesperados: a divisão do armazém seguindo critérios pré-estabelecidos impede atribuir mais operadores a um setor específico, o que pode gerar um volume de trabalho desigual.
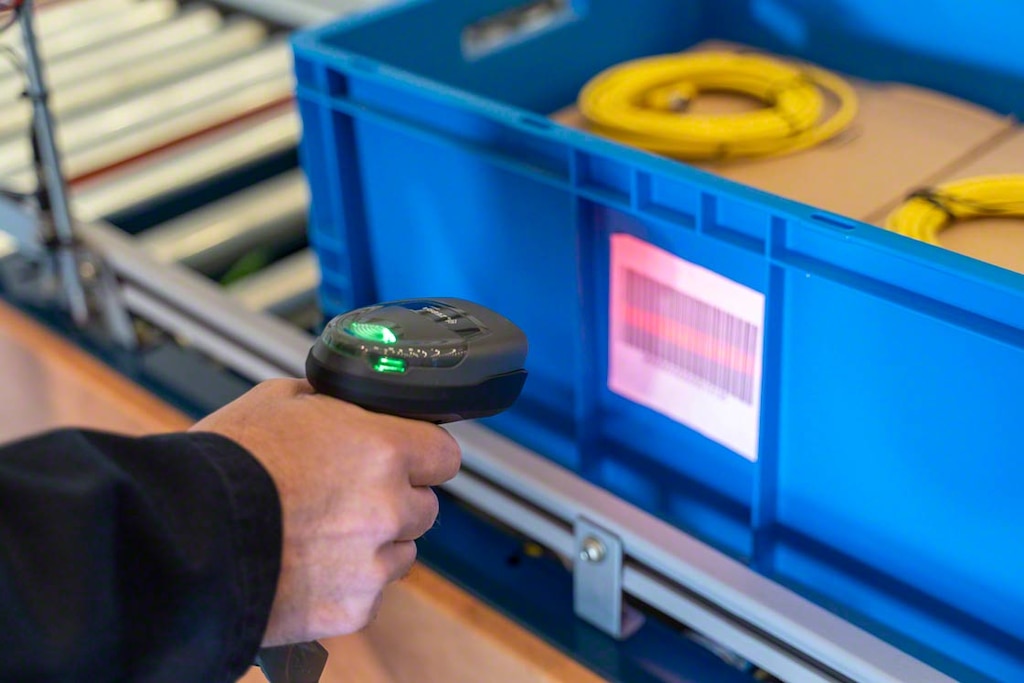
Como implementar o picking por área em um armazém
O primeiro passo para implantar a preparação de pedidos por áreas é reformular o layout do armazém, dividindo-o em diferentes áreas em função de critérios logísticos como a demanda de produtos, as condições de armazenamento ou outras regras.
Além disso, para que o picking por área seja eficaz é necessário contar com um software de gerenciamento de armazém (WMS) que coordene o movimento dos operadores e da mercadoria de forma automática, ou seja, o sistema se encarrega de organizar todas as fases de picking. O operador, equipado com sua pistola de radiofrequência, apenas tem que escanear a etiqueta do contêiner para verificar as referências (SKU) atribuídas a esse pedido para colocá-las no contêiner. De fato, o WMS substitui todo o trabalho manual de gerenciamento: centraliza todas as ordens de pedido, gerencia as localizações dos artigos em função de regras e critérios preestabelecidos, organiza as áreas do armazém e, finalmente, indica, passo a passo, os produtos que devem ser coletados e o contêiner em que devem ser localizados.
Por outro lado, é importante que o Sistema de Gerenciamento de Armazém escolhido seja capaz de automatizar o slotting (o gerenciamento de localizações) das referências. Dessa forma, o software indica ao operador a localização em que deve ser colocada cada referência seguindo critérios previamente estabelecidos pelo responsável logístico.
Para complementar o processo de digitalização, também pode ser conveniente substituir os equipamentos de movimentação manuais e os carros por sistemas automatizados como os transportadores para caixas. Esses equipamentos interligam as áreas do armazém, agilizando o movimento dos contêineres. De fato, o armazém normalmente é projetado com as áreas de armazenamento de produtos de alta rotatividade situadas perto dos equipamentos automatizados visando acelerar a circulação da mercadoria para o posto de trabalho onde os pedidos são consolidados e embalados.
Caso a instalação não esteja automatizada, o picking por área seria realizado com carros, carros menores com localizações para cada pedido, roll containers ou máquinas coleta-pedidos (preparadoras de pedidos).
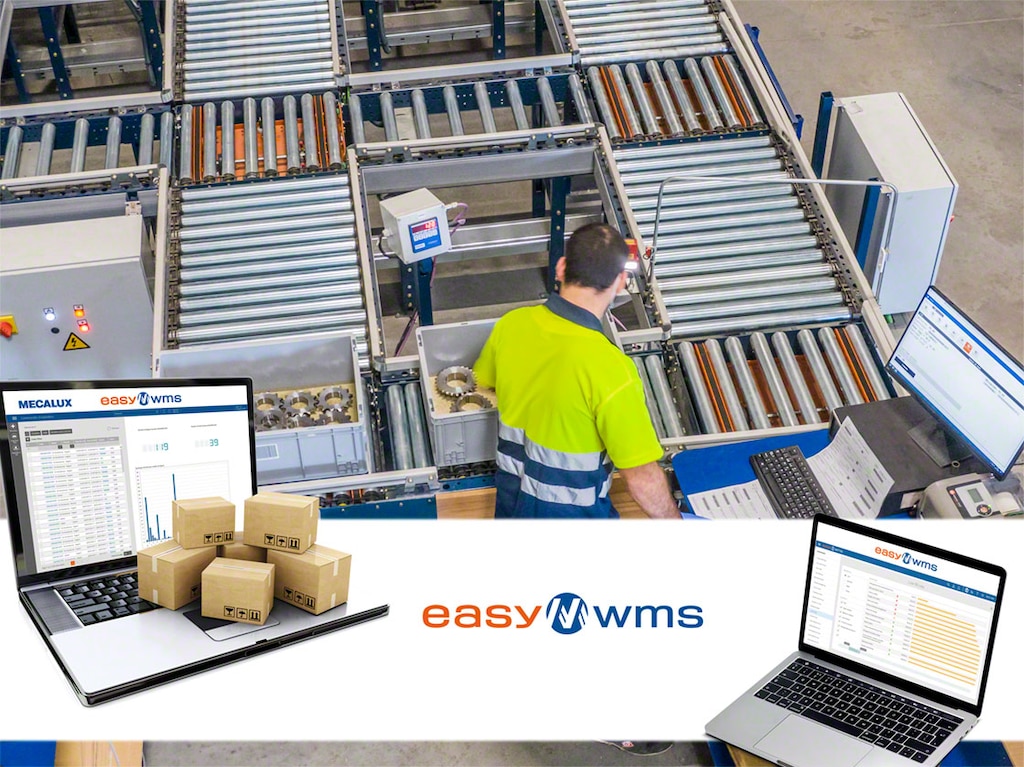
Fazer o zoneamento do armazém de acordo com critérios logísticos
O picking por área é um método de preparação de pedidos muito utilizado em empresas com uma alta quantidade de referências no armazém, porque evita movimentos desnecessários ao atribuir a cada operador uma área. No entanto, para ser colocado em prática é necessário implantar um software de gerenciamento de armazém que coordene os movimentos de mercadorias e operadores, eliminando os erros decorrentes do gerenciamento manual.
Se você estiver interessado em melhorar a eficiência de sua preparação de pedidos, não hesite em entrar em contato conosco. O Sistema de Gerenciamento de Armazém da Mecalux, Easy WMS, é perfeito para automatizar os processos em seu armazém, do picking ao slotting.