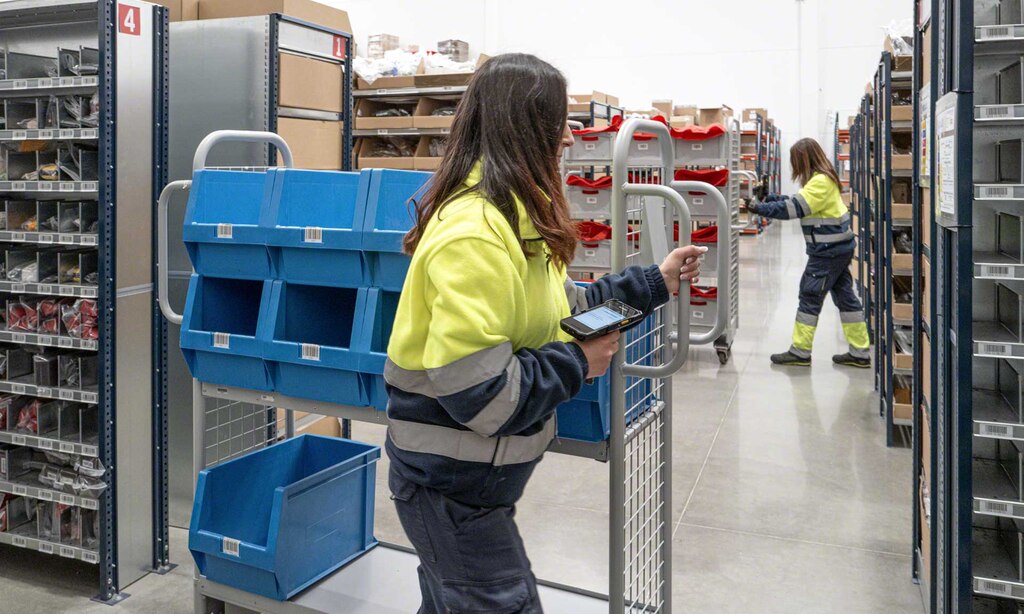
PESQUISA LOGÍSTICA
Por Shuya Zhong, Vaggelis Giannikas, Jorge Merino, Duncan McFarlane, Cheng Jun e Shao Wei
O picking e o packing são dois processos principais ao concluir pedidos. O picking envolve a coleta de vários artigos alojados em diferentes localizações do armazém e o packing coloca-os em embalagens como caixas, sacos ou pacotes. Ambas as operações são cruciais para determinar quanto tempo um pedido ficará nas instalações desde o momento em que o cliente compra uma série de produtos até que esteja pronta para ser expedido.
Neste estudo, analisamos os resultados do planejamento conjunto de picking e packing em armazéns de comércio eletrônico. Estabelecer a sua utilidade exige ter em conta ambas as tarefas: melhorar apenas uma destas atividades não tem um grande impacto, uma vez que estão intrinsecamente ligadas.
No entanto, e embora se trate de duas operações intimamente vinculadas entre si, o picking e o packing são muitas vezes processos sucessivos, mas independentes, realizados por duas equipes de colaboradores diferentes. Propomos que o gerenciamento conjunto do picking e do packing melhora o desempenho dos armazéns em comparação com a organização de ambas as operações separadamente.
Três questões-chave
O objetivo não é apenas melhorar o picking e o packing, mas também reduzir os tempos de espera entre os dois. Para isso, foram utilizadas duas métricas principais: o tempo de processamento do pedido (o tempo necessário para que um único pedido seja preparado para expedição) e a duração do ciclo de produção (o tempo necessário para o armazém processar um determinado número de pedidos até que estejam prontos para envio).
Em um armazém de e-commerce, geralmente, um pedido é classificado em uma das quatro categorias a seguir com base no número de referências e na quantidade solicitada de cada uma: 1-referência-1-artigo, 1-referência-artigos múltiplos, múltiplas-referências-1-artigo e referências-múltiplas-artigos-múltiplos. Esta classificação afeta as localizações a visitar e o tempo de preparação e embalagem.
A pesquisa também considera os diferentes níveis de pessoal designado para picking e packing. Para avaliar os potenciais benefícios de operar de forma integrada, desenhamos um estudo experimental de uma empresa de armazenamento com base em dados empíricos e comparamos o planejamento conjunto de picking e packing com o planejamento individual através de um modelo matemático.
Gerenciar o picking e o packing em conjunto melhora o desempenho dos armazéns
O modelo matemático procurou responder a três questões: Como os pedidos deveriam ser agrupados para formar um picking list? Como os pickers devem ser organizados? Como e em que ordem os picking lists devem ser atribuídos aos encarregados de packing após a conclusão da picking?
Para isso, estabelecemos as seguintes características de um armazém, inspirados em estudos realizados sobre o assunto e nas operações de uma determinada empresa. Assim, essas instalações operam com um sistema de preparação de pedidos a baixo nível onde os produtos são classificados à medida que são coletados. A área de picking inclui vários corredores amplos e um armazém onde cada referência é armazenado em uma única localização. Os pickers usam um carrinho, sempre há um disponível, e realizam rotas em forma de S enquanto os packers permanecem em seus postos de trabalho.
Quatro cenários diferentes
O armazém manual estudado é uma plataforma logística que opera para uma empresa de varejo online. Foram analisados diversos cenários com diversos volumes de pedidos. Cada um necessitava de quantidades e referências diferentes, e também eram divididos entre um número variável de picking lists.
Tempos de espera e execução de picking e packing com métodos integrados e não integrados
Se houver mais packers do que pickers, o ganho de tempo ocorre antes de iniciar a picking
- Com 300 pedidos e um máximo de 24 picking lists, a organização conjunta do picking e packing reduziu o tempo de processamento e a duração do ciclo de produção. Para conseguir isso, o método integrado “sacrifica” parte da eficiência no picking para obter economias significativas de tempo na fase de packing.
- Em cenários para 100-600 pedidos distribuídos entre 8 e 48 picking lists, mostra-se que à medida que o número de pedidos aumenta, os benefícios de gerenciar o picking e o packing em conjunto geralmente diminuem.
- Ao estudar 300 pedidos com diferentes composições - onde varia a proporção de 1-referência-1-artigo, 1-referência-múltiplos-artigos, múltiplas-referências-1-artigo e múltiplas-referências-múltiplos-artigos, observa-se que o método integrado aumenta o desempenho. A vantagem é mais significativa quando a complexidade dos envios a preparar é moderada.
- É distribuído a doze trabalhadores de diversas formas para variar o número de pickers e packers enquanto atende 300 pedidos com 24 picking lists. Quando há mais pickers que packers, o maior benefício da integração está na redução do tempo antes de chegar à fase de embalagem. Se houver mais packers que pickers, a economia de tempo ocorre antes do início do picking. Isto significa que, em alguns cenários onde a embalagem não pode ser acelerada, organizar a picking e o packing em conjunto não traz benefícios.
Resultados: ondas de picking menores
Nossos resultados indicam que o planejamento conjunto de picking e packing pode otimizar o desempenho sob diversas condições. Foi demonstrado que focar apenas nas mudanças de picking não garante melhorias em todo o sistema quando a embalagem continua a atuar como um gargalo. Além disso, pequenos compromissos no gerenciamento do picking podem gerar maiores poupanças de tempo na fase de embalagem e aumentar a eficiência global.
Da mesma forma, o número de pedidos considerado para a distribuição do trabalho e as vantagens que o planejamento conjunto pode proporcionar são inversamente proporcionais. Isto destaca a importância de estabelecer quantos pedidos devem ser agrupados antes de iniciar qualquer processo, como o picking por ondas. Assim, na prática, pode ser preferível optar por múltiplas ondas menores, de modo a obter o maior benefício do planejamento conjunto.
AUTORES DA PESQUISA:
- SHUYA ZHONG. Professora adjunta de Logística e Cadeia de suprimentos na Universidade de Bath (Reino Unido).
- VAGGELIS GIANNIKAS. Professor de Tecnologia e gerenciamento de operações e diretor do Centro de Sistemas Inteligentes de Armazenamento e Logística da Universidade de Bath (Reino Unido).
- JORGE MERINO. Pesquisador adjunto do Instituto de Fabricação da Universidade de Cambridge (Reino Unido).
- DUNCAN McFARLANE. Catedrático de Engenharia de Informação Industrial no departamento de Engenharia da Universidade de Cambridge e diretor do Laboratório de Informação Distribuída e Automação do seu Instituto de Fabricação (Reino Unido).
- JUN CHENG. Shenzhen YH Global Supply Chain Co., Ltd (China).
- WEI SHAO. Shenzhen YH Global Supply Chain Co., Ltd (China).
Publicação original:
Zhong, Shuya, Giannikas, Vaggelis, Merino, Jorge, McFarlane, Duncan, Cheng Jun, Shao Wei. 2022. "Evaluating the benefits of picking and packing planning integration in e-commerce warehouses". European Journal of Operational Research, 301 (Elsevier).
Versão de acesso aberto disponível aqui.