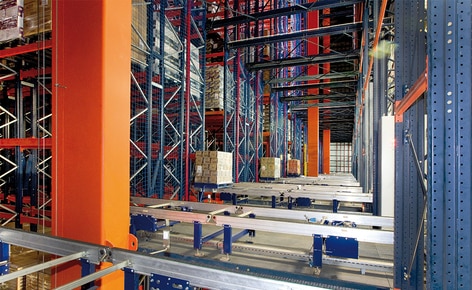
A industria alimentícia Grupo Siro multiplicou sua capacidade e produtividade com um armazém automático autoportante de 35,50 m de altura
Grupo Siro segue em crescimento com um grande armazém automático autoportante

A Mecalux construiu um armazém autoportante de grandes dimensões completamente automatizado para o Grupo Siro, uma das maiores empresas do setor de alimentação na Espanha. Esse inovador centro logístico faz parte da aposta do Grupo em adotar soluções eficientes através da tecnologia como fonte de eficiência e crescimento sustentável.
Quem é o Grupo Siro
O Grupo Siro é um dos fabricantes de bolachas, massas, pão de forma, confeitaria e cereais mais importantes da Espanha.
Foi constituído em 1991 com a aquisição das Bolachas Siro da Danone e desde então sempre apostou na inovação e no uso da tecnologia em todos os seus processos operacionais, com a finalidade de oferecer produtos da melhor qualidade ao melhor preço.
Atualmente, fabrica mais de 300 produtos diferentes e conta com 13 centros de produção, um armazém logístico, um centro de PD&i, um centro de valorização de subproduto, dois centros compostos por escritórios e a sede da Fundação Grupo Siro.
Necessidades do cliente
A empresa registrou um grande crescimento nos últimos anos, especialmente devido à enorme demanda de seu cliente principal: a cadeia de supermercados Mercadona.
Em certo momento, esse crescimento e o consequente aumento da produção aumentaram as necessidades do espaço de seus armazéns, localizados geralmente dentro das próprias fábricas. Para manter o ritmo de produção, a princípio a empresa optou na contratação de armazéns externos, mas isso dificultava a coordenação de sua cadeia logística e aumentava os custos operacionais.
Decidido a apostar em soluções eficientes que respondessem às suas necessidades e impulsionar seu crescimento, o Grupo Siro encomendou à Mecalux a construção de um novo centro logístico em sua sede central em Venta de Baños (Palencia) com duas premissas muito claras: melhorar a capacidade de armazenamento de suas fábricas e fomentar a eficiência e produtividade da empresa.
A solução proposta
O departamento técnico da Mecalux, em colaboração com a equipe logística do Grupo Siro, analisou detalhadamente as necessidades, os fatores condicionantes e possibilidades, até finalmente encontrar a solução adequada: a construção de um armazém autoportante de 36 m de altura que utiliza transelevadores e transportadores controlados pelo software de gestão de armazéns Easy WMS da Mecalux.
O centro logístico está estrategicamente localizado dentro de um círculo de raio de 3 km onde se encontram quatro de suas principais fábricas e a menos de 100 km de distância de outras três, o que facilita e agiliza o transporte da carga entre as fábricas e o centro logístico.
O fluxo de movimentos é muito intenso e contínuo, por isso foram colocadas duas docas de recebimento em uma lateral do armazém, afastadas das nove docas de expedição para não interferir entre as duas operações, com um amplo espaço que permite um movimento mais dinâmico nas manobras de transporte e na espera dos caminhões.
O edifício adjacente ao armazém está constituído por dois pisos diferentes com a finalidade de organizar adequadamente as diferentes operações realizadas:
- O piso inferior destina-se principalmente ao recebimento e à expedição da mercadoria, com uma ampla área de pré-cargas no solo.
- No piso superior, os paletes provenientes das docas do nível inferior entram no armazém. Também há uma área dedicada às tarefas de picking.
O armazém automático do Grupo Siro permite trabalhar de forma ágil e flexível com um custo operacional mínimo
O armazém
O armazém dispõe de dimensões consideráveis:102 m de comprimento, 57 m de largura e 35,5 m de altura, o máximo admitido pelas normativas locais. Distribuído em oito corredores com estantes de profundidade dupla em ambos os lados, cada uma com 14 níveis de carga de diferentes alturas adaptadas aos formatos dos paletes do Grupo Siro: cinco níveis para europaletes de 1.400 mm de altura, oito de 2.000 mm e um de 2.500 mm. As unidades de carga têm um peso médio de 800 kg e um máximo de 1.000 kg.
Cada corredor está equipado com um transelevador bicoluna com garfos telescópicos e uma cabine de manutenção fixada no berço. Essa máquina encarrega-se de armazenar cada palete em sua localização correspondente em função de seu tamanho e de sua rotatividade.
A automatização do armazém é completada com dois circuitos de transportadores: um no térreo onde são depositados os paletes destinados às expedições, e outro no piso superior, a 6,7 m de altura, que interliga todas as entradas e saídas à área de picking.
Na parte superior do armazém os espaços livres entre as treliças foram aproveitados para posicionar os dutos de ar condicionado que regulam a temperatura das instalações distribuindo corretamente o ar.
No exterior do edifício, na parte posterior, foram disponibilizados quatro equipamentos de bombeamento do sistema contra incêndios e um depósito de água com capacidade suficiente para as dimensões do armazém. No interior se encontram os sprinklers e detectores que evitam qualquer início de incêndio.
O piso térreo
Distribuição do piso térreo:
- Doca de descarga automática
- Doca de descarga convencional
- Docas de carga (9 em total)
- Área de controle de entrada de paletes e elevador
- Saídas de paletes do armazém
- Pré-cargas no solo
- Circuito virtual de empilhadeiras LGV
- Acúmulo de paletes vazios
- Recebimento e condicionamento de paletes de entrada
Entrada de mercadoria
A entrada das mercadorias provenientes dos diferentes centros de produção mais próximos é realizada nas duas docas de recebimento, uma delas através de descarga automática dos caminhões e outra de forma manual utilizando empilhadeiras ou transpaleteiras.
A área de descarga tem uma capacidade de acúmulo de dois caminhões completos, ou seja, um total de 66 paletes que se dirigem à área de inspeção onde seu estado é validado.
Todos os paletes passam obrigatoriamente pela área de inspeção, onde se verifica que estejam em bom estado e se seu peso e suas medidas correspondem aos requisitos de qualidade exigidos no armazém. Se o palete for correto, o sistema de controle emitirá a ordem para que siga seu caminho até o elevador, que o transferirá ao piso superior, entrando no armazém automático.
Quando o palete não superar o controle, pode dirigir-se a três áreas diferentes, dependendo da anomalia detectada:
- A área de recondicionamento.
- A área de compactação, onde se corrigem os desabamentos que ultrapassem os limites previstos.
- A remontagem de paletes: quando as unidades de carga dispõem de uma base inadequada, são colocadas em cima de outra em bom estado através dos elevadores. Esses paletes retornam à área de inspeção e são novamente verificados antes de terem acesso ao piso superior.
O palete defeituoso que não tenha nenhuma possibilidade de ser corrigido, será transportado até a área de saída e retirado do circuito.
Os paletes que foram recondicionados voltam a cruzar o posto de inspeção para novamente verificar se cumprem os requisitos do armazém.
É necessário garantir que a mercadoria enviado ao armazém automático seja a adequada, assim como é necessário verificar se a carga não vai transbordar além do previsto.
Saídas do armazém / Expedições
As empilhadeiras de direcionamento automático (LGV) manuseiam os paletes que saem do armazém recolhendo-os nos pontos de saída de cada corredor de armazenamento e transportando-os para a área de espera atribuída em alguma das nove docas de carga, seguindo um circuito virtual previamente programado.
A empilhadeira define sua trajetória ao emitir um sinal de laser que é desviado aos defletores colocados em pontos próximos do percurso. O sistema de gestão pode saber sua posição exata emitindo a ordem para se dirigir às estações de carga quando o nível de baterias chegar a um limite estabelecido. Ao ser uma conexão totalmente automática, não é necessária a intervenção humana durante esse processo.
Apenas a carga dos caminhões é realizada pelos operadores que, operando transpaleteiras, colocam a mercadoria no caminho atribuído pelo software de gestão do armazém em função do número de pedido, a rota a efetuar, o cliente, etc.
O pessoal confirma cada operação e cumprimento das ordens através de um terminal de radiofrequência.
Entrada no armazém
A mercadoria proveniente das docas de recebimento, depois de ter passado pela área de inspeção, tem acesso ao primeiro piso através do elevador.
A partir desse momento, um transportador principal distribui as referências pelos transportadores de entrada nos diferentes corredores de armazenagem. Trata-se um circuito de direção única, pelo qual também se deslocam os paletes que saem dos corredores e se dirigem às áreas de picking.
Organização do piso superior:
- Elevador
- Circuito interno do armazém
- Transportadores de entrada ou saída de cada corredor
- Lançadeira da área de picking
- Postos de picking
- Área de embalagem e recondicionamento
- Transportador principal de entrada no armazém
Área de picking
Da mesma forma, foram instalados dois postos de picking unidos onde cada operador pode preparar dois pedidos ao mesmo tempo. A área está preparada para ser ampliada futuramente se as necessidades do Grupo Siro assim o exigirem.
Os postos de picking estão colocados sobre transportadores. Em ambos os lados do operador se encontram as mesas de elevação hidráulicas que se ajustam a uma posição ergonômica para manusear a mercadoria. Dessa forma, a preparação de pedidos é muito mais ágil.
Cada posto de picking dispõe de um circuito de acúmulo. Também foram disponibilizados empilhadores de paletes e paleteiras que abastecem a área, assim como estações de espera de paletes que saíram do armazém e não têm uma localização livre no circuito do posto atribuído.
Após a finalização do pedido, o palete é incorporado ao circuito de transportadores que, depois de passar pela enfardadeira, se encarregará de transferi-lo novamente ao armazém até que o sistema de gestão ordene sua expedição.
O software
O armazém é gerenciado através do software Easy WMS da Mecalux que se comunica constantemente com o sistema de planejamento de recursos do Grupo Siro, com a intenção de controlar, coordenar e informar sobre todos os processos logísticos e operações desenvolvidas dentro do armazém.
O software foi concebido com um caráter prático e operacional, além de realizar estas funções:
- Controle absoluto sobre a gestão do armazém.
- Gestão da entrada e saída da mercadoria das docas de carga e descarga.
- Colocação estratégica das unidades de carga no armazém seguindo um controle dos corredores e de suas localizações.
- Registro e ajuste do estoque em tempo real.
- Desenho da ordem de saída da mercadoria e sua posterior carga no caminhão através de um terminal de radiofrequência.
- Otimização das tarefas de acordo com o percurso de picking.
- Comunicação direta com o fornecedor logístico do Grupo Siro.
- Coordenação de todos os dados mestre (artigos, proprietários, fornecedores, clientes, etc.).
Benefícios para o Grupo Siro
- Economia nos custos operacionais: a eliminação dos armazéns externos e a centralização das operações no mesmo centro logístico repercute [4]no aumento da produtividade proporcionando um rápido retorno do investimento.
- Máxima capacidade: a elevada altura do armazém e o uso de transelevadores permitiu multiplicar a capacidade de armazenamento do Grupo Siro, adequando-se assim ao crescimento de sua produção.
- Gestão totalmente automatizada: o Grupo Siro integrou e coordenou suas operações de recebimento, armazenamento, picking e expedição de mercadorias em um único espaço, sob a gestão e o controle do Easy WMS, otimizando o desempenho de toda sua cadeia logística.
- Aumento da segurança: os armazéns automáticos oferecem a máxima proteção para os operadores e a mercadoria, contribuindo assim com os objetivos da empresa para fomentar processos eficientes que garantam a todo o momento a segurança das pessoas.
Centro logístico automático do Grupo Siro, Espanha | |
---|---|
Capacidade total: | 40.320 paletes |
Dimensões do palete: | 800 x 1.200 x 1.400 / 2.000 / 2.500 mm |
Peso máximo do palete: | 1.000 kg |
Nº de estantes: | 16 de profundidade dupla |
Nº de corredores: | 8 |
Número de transelevadores: | 8 |
Número de níveis de carga: | 14 |
Comprimento do armazém: | 101 m |
Largura do armazém: | 57 m |
Altura do armazém: | 33,5 m |
Galeria
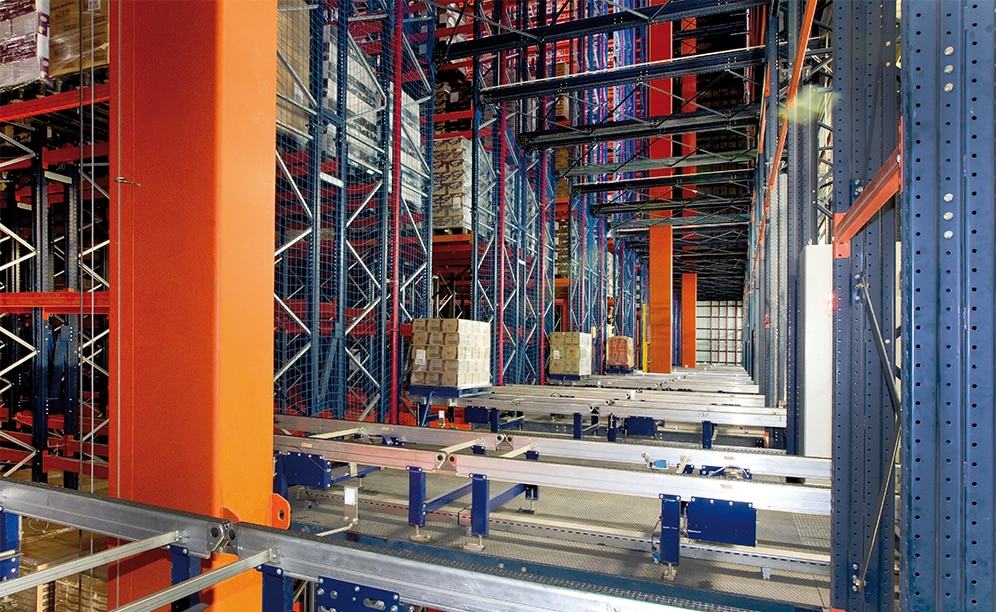
A Mecalux construiu um armazém autoportante de grandes dimensões completamente automatizado para o Grupo Siro
Fale com um especialista